Industry 4.0 is fundamentally transforming the manufacturing landscape, heralding a new era where digital technologies converge to create smarter, more efficient, and highly interconnected factories.
This paradigm shift, often referred to as the Fourth Industrial Revolution, is characterized by the integration of advanced technologies such as the Internet of Things (IoT), artificial intelligence (AI), big data analytics, and automation into every aspect of manufacturing. These innovations are not just incremental improvements; they represent a holistic rethinking of how factories operate, leading to unprecedented levels of productivity, flexibility, and agility.
The Pivotal Role of IoT in Industry 4.0
At the heart of Industry 4.0 lies the Internet of Things (IoT), a network of interconnected devices that communicate and share data in real-time. In the context of manufacturing, IoT enables the seamless integration of physical and digital systems, allowing machines, tools, and even products to interact with each other and with human operators. This interconnectedness facilitates the creation of smart factories, where data-driven insights are leveraged to optimize production processes.
For instance, IoT sensors embedded in machinery can continuously monitor performance, detect anomalies, and predict maintenance needs before they lead to costly downtime. This predictive maintenance capability not only enhances operational efficiency but also extends the lifespan of critical equipment. Furthermore, IoT enables real-time tracking of inventory, streamlining supply chain management and reducing waste. The result is a more responsive and resilient manufacturing process that can adapt to changing market demands with agility.
AI and Big Data: The Brainpower Behind Smart Manufacturing
Artificial intelligence (AI) and big data analytics are the driving forces behind the intelligence of Industry 4.0 factories. As factories generate vast amounts of data through IoT devices, the challenge lies in making sense of this data to drive actionable insights. This is where AI comes into play, with its ability to process and analyze large datasets at unprecedented speeds.
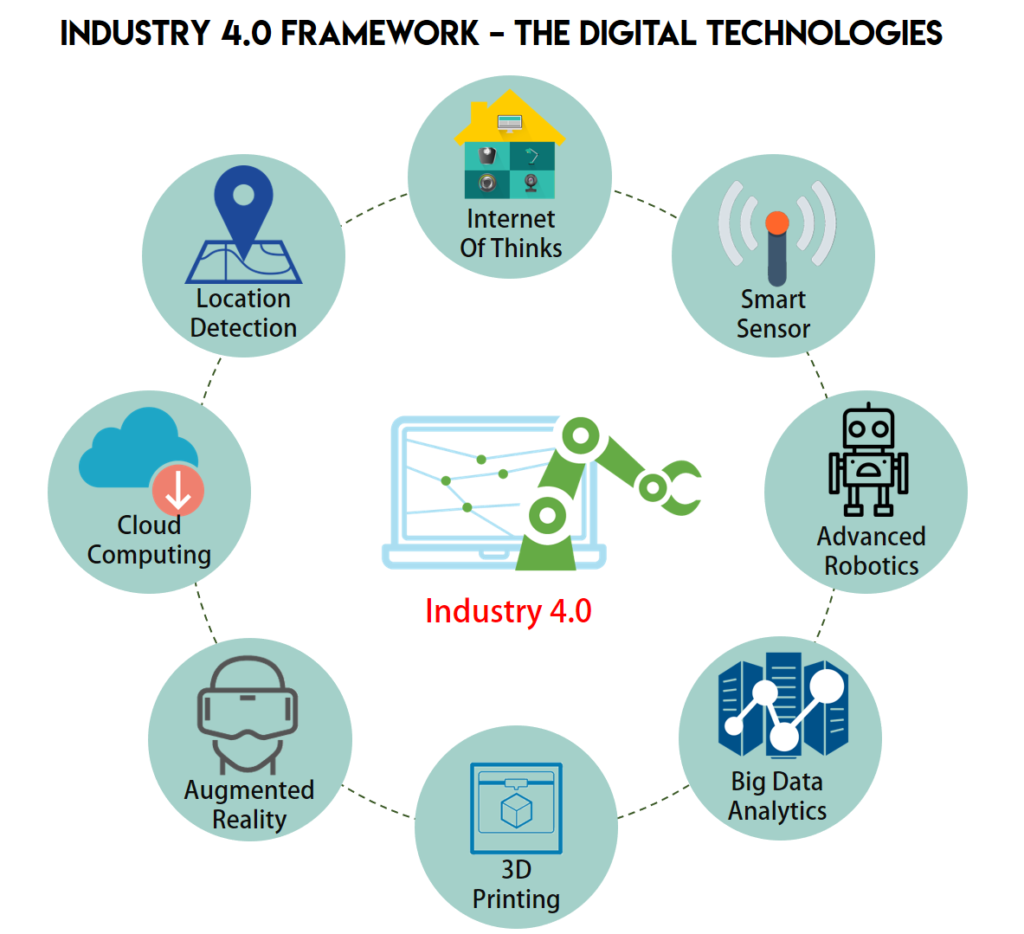
AI algorithms can identify patterns, predict outcomes, and optimize processes in ways that were previously impossible. In the context of manufacturing, AI can be used to optimize production schedules, reduce energy consumption, and even design new products. For example, AI-driven systems can predict fluctuations in demand and adjust production accordingly, minimizing overproduction and reducing costs. Additionally, machine learning algorithms can continuously improve their performance based on new data, leading to ever-increasing levels of efficiency.
Big data analytics further complements AI by providing the tools needed to analyze and visualize the complex data generated by smart factories. By combining AI with big data, manufacturers can achieve a level of precision and customization that was previously unattainable, enabling them to meet customer demands more effectively and stay ahead of the competition.
Automation: Redefining the Manufacturing Workforce
Automation is a cornerstone of Industry 4.0, transforming traditional manufacturing processes into highly efficient, scalable, and flexible operations. The rise of robotics and AI-driven automation technologies allows factories to automate repetitive, dangerous, or labor-intensive tasks, freeing up human workers to focus on higher-value activities such as innovation, problem-solving, and strategic decision-making.
In an Industry 4.0 environment, automation is not limited to individual machines or processes. Instead, it encompasses the entire production line, where interconnected systems work together to optimize output. For example, collaborative robots, or cobots, can work alongside human operators, enhancing productivity without compromising safety. Automated guided vehicles (AGVs) can transport materials across the factory floor with precision, reducing the risk of human error.
The impact of automation extends beyond the factory floor. By automating administrative tasks such as scheduling, quality control, and supply chain management, manufacturers can achieve greater operational efficiency and reduce overhead costs. However, this shift also poses challenges, particularly in terms of workforce adaptation. As automation takes on more roles traditionally performed by humans, there is a growing need for reskilling and upskilling workers to thrive in this new environment.
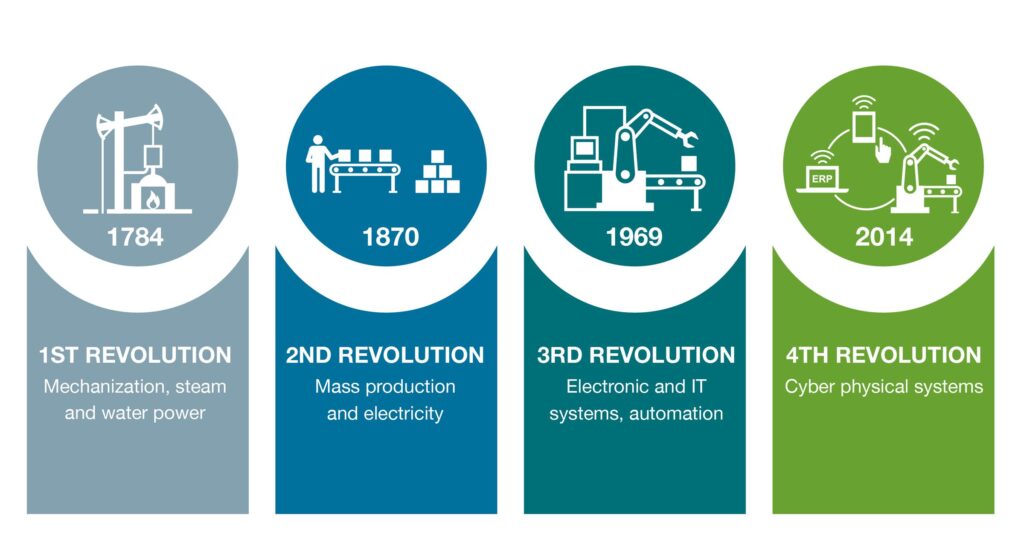
Navigating the Challenges and Opportunities of Digital Transformation
The digital transformation of factories under Industry 4.0 presents a wealth of opportunities, but it also comes with its own set of challenges. One of the primary challenges is the significant investment required in digital infrastructure, including IoT devices, AI systems, and cybersecurity measures. For many manufacturers, particularly small and medium-sized enterprises (SMEs), the cost of adopting these technologies can be prohibitive.
Moreover, the transition to Industry 4.0 requires a cultural shift within organizations. Employees at all levels must embrace new ways of working, and leadership must be committed to driving this change. Resistance to change, coupled with a lack of digital skills, can hinder the successful implementation of Industry 4.0 initiatives.
Cybersecurity is another critical concern. As factories become more interconnected and reliant on digital systems, they become more vulnerable to cyberattacks. Protecting sensitive data and ensuring the integrity of production processes are paramount, requiring robust cybersecurity strategies and continuous monitoring.
Despite these challenges, the opportunities presented by Industry 4.0 are vast. Companies that successfully navigate this transformation can achieve significant competitive advantages, including increased efficiency, reduced costs, and the ability to innovate rapidly. Moreover, the shift towards smart manufacturing aligns with broader trends such as sustainability, as Industry 4.0 technologies can help reduce energy consumption, minimize waste, and create more sustainable production processes.
The Future of Manufacturing in the Industry 4.0 Era
As Industry 4.0 continues to evolve, the future of manufacturing is set to become increasingly digital, interconnected, and intelligent. The concept of the smart factory, where every element of the production process is optimized through technology, will become the standard. In such factories, data will flow seamlessly between machines, systems, and humans, enabling real-time decision-making and continuous improvement.
Looking ahead, we can expect to see further advancements in AI, IoT, and automation technologies, driving even greater levels of efficiency and customization in manufacturing. Additionally, the integration of new technologies such as 5G and edge computing will enhance the connectivity and responsiveness of smart factories, enabling faster and more reliable data exchange.
The companies that embrace these changes and invest in their digital transformation will be well-positioned to lead the next wave of industrial innovation. In contrast, those that fail to adapt may find themselves struggling to compete in an increasingly digital and automated world.
Frequently Asked Questions (FAQ) about Industry 4.0
Q1: What is Industry 4.0?
A: Industry 4.0, also known as the Fourth Industrial Revolution, refers to the ongoing automation of traditional manufacturing and industrial practices using modern smart technology. It is characterized by the integration of IoT, AI, big data, and cloud computing to create smart factories.
Q2: How does Industry 4.0 benefit factories?
A: Industry 4.0 enhances factory efficiency through automation, real-time data analytics, and improved communication between machines. This leads to reduced production costs, increased productivity, improved product quality, and the ability to quickly respond to market changes.
Q3: What role does IoT play in Industry 4.0?
A: IoT enables interconnected devices to communicate and share data across the production process. In Industry 4.0, IoT helps monitor equipment, predict maintenance needs, optimize energy usage, and improve overall operational efficiency.
Q4: How does AI contribute to Industry 4.0?
A: AI contributes by enabling predictive maintenance, optimizing supply chains, automating complex tasks, and providing valuable insights from data analysis. AI-driven systems help factories make data-informed decisions that enhance efficiency and reduce errors.
Q5: What are the challenges of implementing Industry 4.0?
A: Key challenges include the high initial investment in technology and infrastructure, the need for skilled labor, cybersecurity risks, and potential job displacement due to automation. Additionally, there may be resistance to change within organizations.
Q6: What is the future of Industry 4.0?
A: The future of Industry 4.0 involves the continued development of smart factories where all production processes are interconnected and optimized through technology. As more companies adopt these practices, Industry 4.0 will lead to greater efficiency, lower costs, and more agile manufacturing capabilities.
Q7: How can businesses start their Industry 4.0 journey?
A: Businesses can start by assessing their current technology landscape, identifying areas where automation and data analytics can add value, and investing in IoT devices and AI-driven systems. Training employees and developing a clear digital strategy are also critical steps in the transition to Industry 4.0.